Calibration of Fourier Transform Infrared Spectrophotometer (FTIR)
1.0 OBJECTIVE
1.1 To lay down a procedure for the Operation and Calibration of Fourier Transform Infrared Spectrophotometer (FTIR).
2.0 SCOPE
2.1 This procedure is applicable for the Operation, Calibration and Maintenance of Fourier Transform Infrared Spectrophotometer (FTIR), used in the Quality Control Department
3.0 RESPONSIBILITY
3.1 QC Officer or QC Executive
4.0. ACCOUNTABILITY
4.1 QC Manager
5.0. PROCEDURE
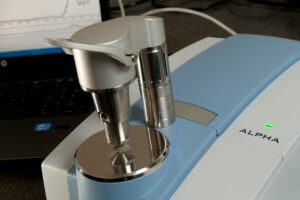
5.1.1 FTIR Spectrophotometry is one of the major Analytical Techniques which are being used in the Pharmaceutical Industry for the Identification
and Assay determination of various materials.
5.1.2 Fourier transform infrared (FTIR) spectroscopy is a measurement technique for collecting infrared spectra. Instead of recording
the amount of energy absorbed when the frequency of the infra-red light is varied (monochromator), the IR light is guided through an interferometer.
After passing through the sample, the measured signal is the interferogram. Performing a mathematical Fourier transform on
this signal results in a spectrum identical to that from conventional (dispersive) infrared spectroscopy.
5.1.3 FTIR spectrometers are cheaper than conventional spectrometers because building of interferometers is easier than
the fabrication of a monochromator. In addition, measurement of a single spectrum is faster for the FTIR technique because the information
at all frequencies is collected simultaneously. This allows multiple samples to be collected and averaged together resulting in an
improvement in sensitivity. Because of its various advantages, virtually all modern infrared spectrometers are FTIR instruments.
5.2 Operation
5.2.1 Before operation ensure that the instrument is clean and calibrated.
5.2.2 Turn ON the main power of the instrument and computer connected with the instrument.
5.2.3 Wait for at least 15 minutes until the initialization succeeded for proper stabilization of the instrument.
5.2.4 Before operation check the sample holder or cleanliness, if it is no clean properly it will contaminate the
Current sample and gives inaccurate results, so clean the sample die or sample holder with acetone or ethanol
and dry with tissue paper.
5.2.5 To run the software double click on the software icon on the computer desktop.
5.2.6 To open the main functioning window enter the individual user ID and password.
5.2.7 Set the general parameters as follow: Resolution : 4 cm⁻1, Measurement mode : % transmittance, No. of
Scans : 1 to 20, Scanning range : 4000 to 400 cm⁻1 or as per requirement.
5.2.8 To execute the background click on the background or reference.
5.2.9 In case of ATR (Attenuated total reflection) assembly, fix the assembly in the sample compartment, ensuring
that sample holder is empty and take air as a background scan the air without any sample in the sample
compartment.
5.3 Cleaning
5.3.1 Before cleaning switch off the instrument, Clean the outer surface of the instrument with dry clean lint free
cloth.
5.3.2 If required then clean the outer surface of instrument with lukewarm water and keep the surface dry.
5.3.3 Clean the sample holder with IPA or methanol and keep the sample holder and sample compartment in a dry
condition.
5.4 Safety and Precaution
5.4.1 Always keep the instrument away from direct sunlight.
5.4.2 Keep the instrument away from areas of high humidity / moisture.
5.4.3 Avoid spilling liquid into the sample compartment. Clean all spills immediately.
5.4.4 Do Not stare into the internal laser beam.
5.4.5 Do Not use a flammable gas to purge the instrument. Only use clean, dry, Oil-free Nitrogen or air to purge the instrument.
5.4.6 Do not attempt to make any adjustments, replacements or repairs to the instrument.
5.4.7 Do not operate the instrument with any cover or part removed.
5.4.8 Make sure that the sample compartment is free from dust and other foreign matter.
5.4.9 Never use the instrument when it is out of calibration.
5.4.10 Activate the silica gel bags kept in the sample compartment at 105º C for 1 hour periodically.
5.4.11 Always clean the IR assembly properly, before and after the analysis.
6.0 ABBREVIATION
Sr. No. |
Abbreviation used |
Extended Form |
2.0 |
QC. |
Quality Control. |
3.0 |
SOP |
Standard Operating Procedure. |
sop for Calibration and Maintenance of Laboratory Instruments and Equipment
Disposal of Residual Sample or Left Over Material
sop for for Laboratory Incident
standard operating procedure temperature monitoring
sop for operation of infrared moisture balance
sop for preparation of mobile phase
sop for Preparation and Issuance of Analysis protocol standard
sop of placebo and impurity stock solutions
sop for disposal of residual sample
sop for handling of pharmacopoeial changes
sop for procedure for operation of ultrasonic cleaner
difference between UPLC and HPLC
sop for for Emergency Eyewash and Shower
sop for operation and calibration of total organic carbon analyzers
sop for operation of cobb tester
sop for Operation and calibration of atomic absorption spectrophotometer
sop for Operation and calibration of gas liquid chromatograph
sop for operation of humidity oven
sop for operation and calibration of serological water bath
sop for monitoring of drain trap
sop for destruction of analytical samples after testing and control samples
sop for destruction of used chemicals
Sop for Operation of suction pump
sop for Operation and calibration uv cabinet
sop for Operation and calibration of bulk density apparatus
sop for operation and calibration of shore hardness tester
sop for operation of rub proofness tester
sop for monitoring of purified water
sop for Retesting of packaging materials
sop for Retesting and resampling of raw materials
sop for Control of issuance of record of analysis green sheets
sop for Control of computer passwords
sop for sampling of packaging materials PM
sop for sampling of sterile raw material
sop for sampling of intermediates and finished products
sop for operation and calibration of friability test apparatus
sop for approval and rejection of packaging materials
sop for non conformance of RM PM and finished product
sop for collection storage and disposal of control samples
sop for trend analysis of finished products
sop for Chromatographic practices and system suitability
SOP For Good Laboratory Practices
sop for cleaning and operation of sieve shaker
general specification of packing material cartons
sop for Password for Analytical Instrument and LIMS software
sop for Rounding off numerical analytical results
sop for sampling of bulk and finished product
sop for cleaning of spillage material
sop for Handling of Reference Standard
sop for hplc column maintenance and washing
procedure for sampling and handling of bulk sample
STP for borewell generation point (raw water storage tank)
sop for preparation and standardization of 0.1M Zinc Sulphate
Operation &calibration of analytical balance (dhona)
Operation and Calibration Procedure for Disintegration Test apparatus
sop for preparation and standardization of 1 M Hydrochloric Acid
Preparation and standardization of 0.1 M ceric ammonium sulphate solution
sop for preparation and standardization of 0.05 m iodine solution
validation of volumetric solution 0.1m ammonium thiocyanate
handling of reference standard and preparation of working standard
sop for water sampling and analysis
sop for operation for validation of excel worksheets
sop for stability of volumetric solutions
sop for preparation of raw material in process finish product packing material data sheets
sop for handling of hazardous chemicals
sop for handling of glassware and allocation of identification number
sop for operation cleaning and calibration of bursting strength tester
sop for rounding off the analytical test results
procedure for Analyst Qualification
sop for operation and calibration of dissolution Apparatus
procedure for maintenance of desiccators
sop for for hplc column receipt checking id no and regeneration
safety data sheet for laboratory chemicals
procedure for handling of poisonous chemicals
sop for cleaning of sampling devices
sop for calibration procedure of instruments
sop for specification and standard testing raw material packing material and finished product
procedure for operation and calibration of potentiometric titrator
procedure for operating and calibration of digital hardness tester
procedure for disposal of expired chemicals, reagents and solvents
sop for behavior in quality control department
sop for preparation and standardization 0.1M sodium thiosulphate
sop for preparation and standardization 0.1M Disodium Edetate
preparation and standardization 0.1M Sodium Hydroxide Solution
Preparation and standardization of 0.1M Perchloric acid solution
sop for preparation 0.05M edetate disodium
sop for preparation 0.1M silver nitrate
sop for Operation and Calibration of High Performance Liquid Chromatography
sop for UV & Visible Spectrophotometer
procedure for Cleaning of laboratory glassware
Cleaning of Instrument, Instrument bench and surrounding area of Quality
Safety Precaution in Quality Control Department
Operation & Calibration of Analytical Balance
Calibration of Glassware in Quality Control Department
handling of samples received in Quality Control
Cleaning and Operation of Refrigerator
Operation, Cleaning and Calibration of water bath
Operation & Calibration of Refractometer
Operation and Cleaning of Centrifuge Apparatus
cleaning, operation & calibration of Vernier caliper
Calibration of Fourier Transform Infrared Spectrophotometer (FTIR)
Cleaning and operation of Moisture Analyzer
Cleaning & Operation of Vacuum pump in Quality Control Department
Operation and Calibration of Polarimeter
Cleaning and operation of Magnetic Stirrer
Cleaning Operation and Calibration of Melting Point
Operation Cleaning and Calibration of Muffle Furnance in Quality Control Department
procedure of operation and Cleaning of Sonicator
Operation Cleaning & Calibration of pH meter in Quality Control Department